How more testing labs than just food safety can reduce risk by adopting HACCP principles and risk-based thinking
Every business must
Risk management and ISO/IEC 17025:2017 accreditation
ISO/IEC 17025:2017 mandates that laboratories develop and execute strategies to manage risks and identify opportunities to enhance operational effectiveness. The standard acknowledges that risk-based thinking has allowed for a decrease in rigid guidelines and their substitution with performance-based criteria.
Risk-based thinking is a structured approach you can use to help make informed decisions for your business by identifying, assessing, and managing risks. Risk-based thinking encompasses the methodical identification, assessment, and control of risks and has the potential to mitigate risk for laboratories of many disciplines.
Specific terms outlined in the ISO/IEC 17025:2017 standard urge
Hazard Analysis and Critical Control Points (HACCP)
Hazard Analysis and Critical Control Points (HACCP) is a US Food & Drug Administration (FDA) food safety management system that is
Applying principles of the FDA HACCP food safety system to your laboratory operations can include processes such as performing hazard analysis, pinpointing critical control points, setting critical limits, setting up monitoring protocols, determining corrective actions, conducting verification, and keeping comprehensive records.
Let’s explore how you can adapt HACCP principles for your laboratory:
Conduct hazard analysis
This phase could be likened to performing risk assessment. The first step involves recognising potential risks within laboratory operations that might jeopardise the accuracy of testing or calibration processes. These risks could encompass issues such as equipment breakdowns, sample contamination, human mistakes, chemical hazards, or compliance concerns.
Identify critical control points
Critical control points (CCPs) are key junctures in laboratory procedures where control measures can be applied to prevent,
Set critical limits
Set specific critical limits at each CCP to define acceptable ranges for factors like temperature, time, cleanliness, calibration schedules, or even level of detail needed in documentation to obtain consistent results. This ensures that processes adhere to predetermined standards to mitigate risks.
Implement monitoring procedures
Monitoring procedures involve regularly observing, measuring, or recording parameters at CCPs to confirm that processes are operating within critical limits. This could involve routine equipment checks, quality control tests, environmental monitoring, data review, proficiency testing, or demonstrating ongoing competence of staff.
Establish corrective actions
In the event of deviations from critical limits or the identification of risks, your lab must take prompt corrective actions to rectify the situation. These actions might include process adjustments, equipment recalibration, sample retesting, and investigating the root causes of deviations to prevent their recurrence.
Verify
Verification ensures that the HACCP plan effectively controls risks and maintains safety in laboratory operations, while validation confirms the scientific soundness and adequacy of control measures. Verify the efficiency of control measures and corrective actions through validation activities, audits, trending of quality control, and reviews to confirm that critical control points operate effectively and that risks are managed appropriately.
Document and retain records
Maintaining detailed records of risk
Embrace risk-based thinking
ISO/IEC 17025 mandates that laboratories implement a methodical approach to risk management. By blending risk-based strategies with established methodologies such as HACCP, laboratories of any discipline can elevate risk management protocols, enhance operational effectiveness, and foster a safe and quality-driven environment. No matter what industries your testing laboratory serves, there are many approaches to successfully integrating risk-based thinking into your laboratory’s operations.
Perry Johnson Laboratory Accreditation, Inc. is a private third-party accreditation body based in the United States that validates the competency of testing and calibration laboratories, inspection bodies, reference material producers and sampling
With Clinisys Laboratory Solution™, your laboratory will have a solid foundation for compliance with government regulations and standards. Built for disciplined data management and reporting, the content packages for Clinisys Laboratory Solution™, like Clinisys Food & Beverage Laboratory™, incorporate the relevant standards, guidelines, and protocols for your industry into your workflows. Automatically align testing procedures, analytical methods, and data analysis with regulatory requirements. With its automated data validation processes, Clinisys Laboratory Solution also proactively flags potential issues or deviations, consistently documents all activities and modifications for exacting traceability and data integrity, and simplifies standards audits, laboratory certification, and regulatory reporting.
Let’s start a conversation about how your LIMS matters for mitigating risk, fostering innovation, and bolstering client and regulatory confidence. Connect with us today to build your lab of the future.
Related content

Why equipping scientists to harness digitalisation is key to driving laboratory innovation
Digital transformation can deliver significant benefits for laboratories and their customers, but success requires more than simply buying the latest technology.
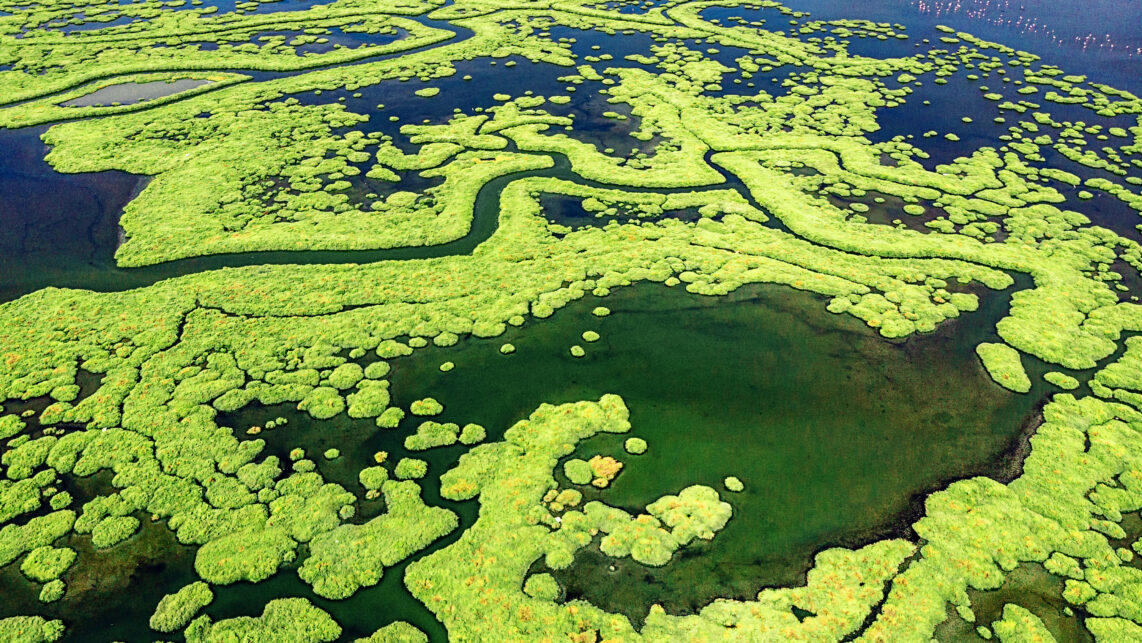
How to put quality first in environmental and water laboratories
Quality assurance and control measures are essential for environmental and water testing laboratories to ensure accurate and reliable data.
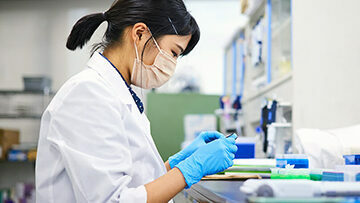
For human health’s sake, labs must take an increasingly holistic approach to data
Specialised testing at US public health laboratories is a vital function, but their resulting test data must increasingly connect and converge to produce a more complete picture of the many factors that affect human health. Learn how PHL data is being connected, shared, integrated, and